The Amalric Walter Research
Project
and subsequent development
Max Stewart
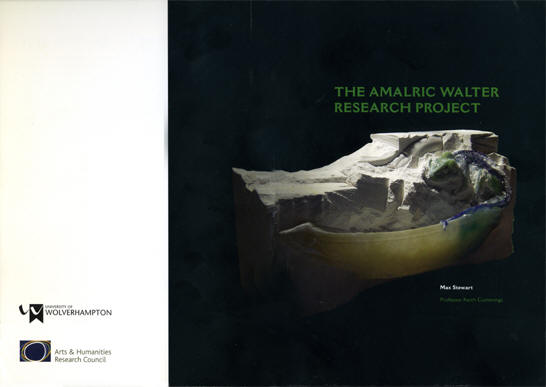
In August 2006 Broadfield House Glass Museum in the UK held the first solo
exhibition of the French pâte de verre artist Amalric Walter (1870-1959)
anywhere in the world. Part of the extraordinary nature of the exhibition was
that it comprised almost in its entirety a single private collection of 161
pieces of Walter’s glasswork, which had been donated for the purpose. This
unique collection is now held in trust by the museum and has been the basis of
two investigations into his methodology and techniques. As a result we have a
much greater understanding of the man and his work. The first enquiry was a
British Arts and Humanities Research Council funded project that ran alongside
the Broadfield House exhibition. Professor Keith Cummings of the University of
Wolverhampton led it and I was the assistant. The second separate enquiry built
on that previous one in the form of my own PhD at Edinburgh College of Art and
Edinburgh University, and was an investigation that involved painstaking
chemical analysis and reproductions of chemically made colour. This article
concentrates on the findings of that second investigation. In all the researches
what was immediately clear was that at the height of his powers in 1925 Walter
was hailed in France as the greatest glassmaker of his generation (Vallaires
1925), yet when he died he was almost forgotten, and his unique style of working
in pâte de verre was lost for two generations.
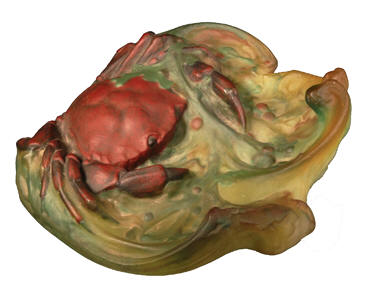
Fig. 1
Part of the mystery surrounding Walter’s work has been how Walter actual made
his pieces. Since his death and loss of his notebooks it has even been doubted
in some quarters whether his work was pâte de verre at all, but was instead
enamelled glass. Certainly, as can be seen in Fig. 1, the main body of the crab
has the appearance not of glass, but of something else, perhaps the matt glaze
of ceramic. My investigation with Keith Cummings at the University of
Wolverhampton during 2005-7 proved this theory to be a false premise. In that
investigation we showed the fine details of his dishes were made in the mould
during the kiln forming process. The detailing – patterns, lines, flowers,
leaves, body details - were all painted into the mould with paints made from
finely ground coloured glass (in essence a glaze) and allowed to dry before
being backfilled with larger particles of glass before the work was fired.
Subsequently, my research has revealed that despite his use of glass as a medium
of expression he was first and foremost a ceramist in his thought processes.
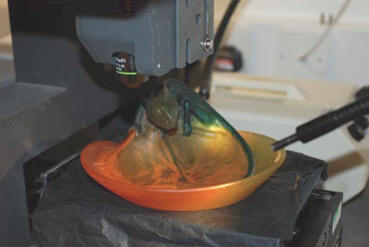
Fig. 2
Under the auspices of Dr Andrea Hamilton of Edinburgh University I was fortunate
to be able to have examined in the laboratories of the National Museum of
Scotland 5 of Walter’s pieces from the collection using a Scanning Electron
Microscope (SEM), an X-ray Fluorescence (XRF) machine and a Raman Spectroscope.
Fig 2 shows one of the works being examined by the XRF machine. The results of
these enquiries indicated three significant results. The first was the presence
of zinc in several of the opaque areas of his work, particularly in the red of
his berries. The second was the presence of uranium and its associated compounds
within the yellow, orange and ochre areas of colour. And, thirdly, the overall
lead content of Walter’s glass.
Zinc is not known as a colorant for glass and is not normally associated with
its formation, although there were zinc based glasses made for a brief period in
the 19th century (Weyl 1999). Zinc (in the form of an oxide) is normally
associated with ceramic glazes especially with the fluxing of iron salts and
their glazes (Hamer 1991). Uranium on the other hand was used from 1840 through
to 1942 both in ceramic glazes and for colouring glass (when its availability to
the general public was halted), the most familiar being the Vaseline glass of
our grandmothers’ (Skelcher 2007). However, its use has not been very much
discussed in lead crystal of which Walter’s work comprises. Under the Raman
spectroscopy all 5 of the Walter pieces showed clearly that lead
(PbO2)
content was around about 42%, not the 50%
as had been previously suggested by
Noël Daum (Daum 1984). This explains why
Walter’s work is less scratched and damaged than it otherwise would be had it
been made with the higher lead content. That produces a softer glass that can
almost be scratched with the fingernail.
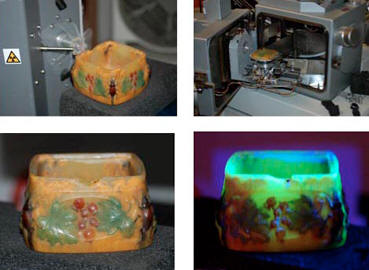
Fig. 3
The appearance of uranium in the examination results was unusual,
as it has not been thought in Britain that any of the pâte de verre artists of
the early 20th century utilised uranium compounds in their work to
make colour. Fig 3 shows the uranium content of a small square powder box by
Walter glowing under UV light during examination. With this discovery it is
clear they did and there are two historic recipes contained with the respective
notebooks of Gabriel Argy Rousseau (1885-1953) and
François Décorchemont
(1880-1971) (Leperlier 1982). Both artists were contemporaries of
Walter and they list respectively ammonium uranate
(NH4)2U2O7
for a yellow-gold colour, and uranium oxide (UO2) for an
emerald green.

Fig. 4a
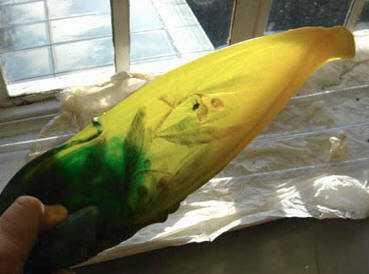
Fig. 4b
These two colours can be seen in the Walter’s famous Chameleon dish (Fig 4a and
b) as well as in other pieces of his work.
How Walter came to use uranium can be only surmised, but it is my belief he was
introduced to it when at Sèvres, and its use was reinforced when he was at Daum
Frères. Baccarat, Lalique, Daum and other glassmaking houses in the Metz region
of France are all known to have used uranium as a colourant in their blown and
cast work (Strahan 2001). That Walter uses the same colour palette throughout
his career, especially maintaining it after Bergé died and his new collaborators
changed his style to the more fashionable style of Art Deco, would indicate
Walter made his own colours in glass. It can be supposed therefore he used
uranium, too, as it was readily available to producers and makers of glass. The
process of introducing it into glass is quite simple, as all that is involved is
the mixing of the compounds into the glass’s raw ingredients and heating it to
founding temperature of around 1270oC.
The discovery of uranium compounds in Walter’s glass led me to examine the whole
of Broadfield House’s 161 piece collection of Walter with a radiation
monitor/Geiger counter. The startling results were that amongst the 161 pieces
all that contained the palette of yellow, orange or ochre - as well as some
pieces that were dark red (sang de beouf) or brown - were radioactive, sometimes
25 times the normal background reading of 2-4 Counts Per Second. None of the
blue or green colours registered on the radiation monitor as having a background
reading of more than 2, sometimes less.
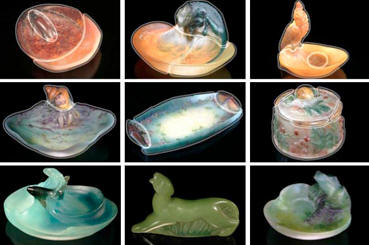
Fig. 5
Some pieces in the Broadfield House Collection of Walter that contain the blues,
yellows and greens together registered mainly in the yellow areas and not in the
blue or green areas. Fig 5 shows an indication as to where radiation is emitted
in the colour spectrum on nine of the Broadfield House collection of Walter.
Alongside this study of uranium in Walter’s work I was fortunate to procure some
uranium oxide, and under the guidance of my supervisor, Dr Andrea Hamilton, some
of it was synthesised to ammonium uranate. Following Argy-Rousseau’s and
Décorchemont’s recipes (quoted above) it and the uranium oxide were placed into
Gaffer Glass crystal frit in ceramic crucibles and heated to founding
temperature.
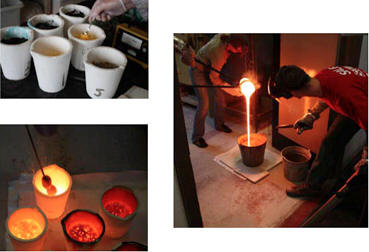
Fig. 6
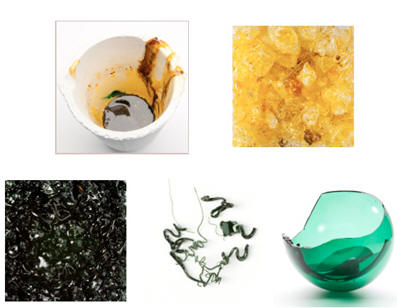
Fig.
7
At 1270°C the contents of crucibles were poured into buckets of cold water (Fig
6) to achieve the colours seen in Fig 7. The colours match exactly the two
colours used by Walter in his work Dish with Lizard from the Broadfield house
collection shown in Fig 8 – a golden yellow and a dark green.
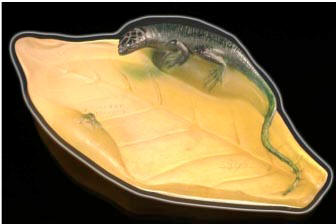
Fig. 8
The fact that he used uranium in his work (as well as zinc) may provide experts
in the future with a test as what is an authentic Walter and what is not.
Uranium oxide and its compounds are strictly controlled by licence throughout
Europe and America, and hard to come by, as I found in my work. The use of zinc
is complex, too, in Walter’s methodology and has proved hard to replicate
exactly. In the meantime a general cataloguing of Walter’s known work would
ascertain what he made and when, as would the discovery of his moulds which are
still somewhere in existence.
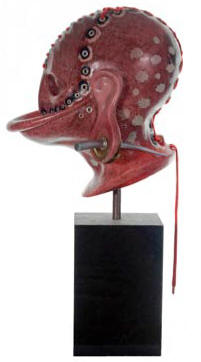
Fig. 9 and 10
Since 2006 it is with certainty that we can now say how Walter made his pâte de
verre. I have occasionally been asked ‘why bother to revive a lost technique?’
and it is true that Walter’s work lies in the glittering past. But discovering
the past has enormous implications for the future. The findings in my PhD and
ultimately in my own pâte de verre work have shown that Walter’s methodology is
also readily applicable to a modern studio artist - as may be seen in Fig 9 and
10. These are two life-sized heads/masks I have made solely using Walter’s
techniques. Over the past 4 years it has been encouraging to see how some
students in the glass departments at the universities of Wolverhampton and
Edinburgh are using elements of his technique to influence their own work. There
is, of course, the danger that by disseminating his methodology forgers will
have an extra tool for deception, and reproductions will continue to evade
detection. The counter argument is that by understanding how Walter’s methods
can be used and expanded upon, a new history for the collectors of the future
can be achieved. And that in the final analysis is the point of reviving lost
techniques. Not just for academic interest, but as one poet said: to craft new
shapes to entrance the world.
Max Stewart
Bibiography:
Vallieres, J. (April 1925) Un grand Verrier francais: M.A. Walter. Le Verre:
Revue mensuelle des industries et du commerce du verre, vol. 5, no. No.4,
pp. 76.
Weyl, W.A. (1999) Coloured glasses. UK, Society of Glass Technology.
Hamer, F.a.J. (1991) The Potter's Dictionary of Materials and Techniques.
3rd ed. London, A and C Black Ltd.
Skelcher, B. (2007) The Big Book of Vaseline Glass. Atglen, PA, USA,
Schiffer Publishing Ltd.
Daum, N. (1984) La pate de verre. Paris, France, Denoel.
Lerperlier, A.e.E. (1982) Technique de la pâte de verre. La Revue de la
Céramique et du Verre, pp. 22-23.
Strahan, D. (2001) Uranium in Glass, Glazes and Enamels: History,
Identification and Handling. Studies in Conservation, vol. 46, no. 3, pp.
181-195.
Related Articles: